Temporary replacements are often seen as short-term solutions to pressing problems, but their importance cannot be underestimated. Whether it's in the workplace, home, or community, understanding how to implement and manage temporary replacements effectively can make a significant difference. This guide will delve deep into the concept of temporary replacement [EP 3], offering insights, strategies, and actionable tips for anyone who needs to navigate this process.
As we move forward in an ever-changing world, the need for adaptability and quick thinking has never been more critical. Temporary replacement [EP 3] is a concept that has evolved over time, becoming a cornerstone of problem-solving in various industries. From human resources to logistics, understanding the nuances of temporary replacements can help organizations and individuals alike maintain stability during challenging times.
This comprehensive guide will explore everything you need to know about temporary replacement [EP 3], from its definition and significance to practical strategies for implementation. By the end of this article, you'll have a clear understanding of how to approach temporary replacements and make the most out of them, ensuring minimal disruption and maximum efficiency.
Table of Contents:
- What is Temporary Replacement?
- Importance of Temporary Replacement
- Biography of Temporary Replacement
- Common Types of Temporary Replacements
- Strategies for Effective Temporary Replacement
- Benefits and Challenges of Temporary Replacement
- Best Practices for Temporary Replacement
- Managing Temporary Replacements in the Workplace
- Case Studies of Successful Temporary Replacements
- Conclusion
What is Temporary Replacement?
Temporary replacement refers to the process of substituting a permanent resource, such as an employee, equipment, or service, with a temporary one to ensure continuity and efficiency. This concept is widely used in various industries, including healthcare, manufacturing, and human resources. Temporary replacement [EP 3] often involves assessing the needs of the organization, identifying suitable candidates or solutions, and implementing them seamlessly.
Key Characteristics of Temporary Replacement
Temporary replacements are typically characterized by their short-term nature and their ability to fill gaps quickly. Below are some key characteristics:
- Flexibility: Temporary replacements can be adjusted based on changing needs.
- Cost-Effectiveness: They often come with lower costs compared to permanent solutions.
- Scalability: Temporary replacements can be scaled up or down depending on demand.
Importance of Temporary Replacement
The importance of temporary replacement [EP 3] cannot be overstated, especially in today's fast-paced world. Organizations often face unexpected challenges, such as employee absences, equipment failures, or service disruptions. Temporary replacements provide a reliable solution to these issues, ensuring that operations continue smoothly without significant interruptions.
Impact on Business Continuity
Business continuity is one of the primary reasons why temporary replacements are essential. By having a well-thought-out plan for temporary replacements, organizations can minimize downtime and maintain productivity. This is particularly crucial in industries where even a brief disruption can have far-reaching consequences.
Biography of Temporary Replacement
Temporary replacement has a rich history that dates back to ancient times. Initially used in agricultural societies to manage labor shortages during harvest seasons, the concept has evolved significantly over the centuries. Below is a brief overview of its development:
Historical Context
Temporary replacement gained prominence during the Industrial Revolution when factories began hiring temporary workers to meet seasonal demands. Over time, the concept expanded to include equipment, services, and even entire systems. Today, temporary replacement [EP 3] is a vital component of modern business practices, supported by advanced technologies and methodologies.
Category | Details |
---|---|
Origin | Ancient agricultural societies |
Key Development | Industrial Revolution |
Modern Use | Various industries, including healthcare, manufacturing, and human resources |
Common Types of Temporary Replacements
Temporary replacements come in various forms, each designed to address specific needs. Below are some of the most common types:
Employee Replacements
Employee replacements are perhaps the most well-known form of temporary replacement. They involve hiring temporary workers to fill in for absent employees, ensuring that operations continue uninterrupted. According to a study by the Bureau of Labor Statistics, the demand for temporary workers has been steadily increasing over the past decade.
Equipment Replacements
Equipment replacements are critical in industries such as manufacturing and construction. When a piece of equipment fails, a temporary replacement can be deployed to maintain productivity. This approach not only minimizes downtime but also allows for proper repair or replacement of the original equipment.
Strategies for Effective Temporary Replacement
Implementing temporary replacements effectively requires a strategic approach. Below are some strategies that organizations can adopt:
Identify Key Needs
The first step in any temporary replacement strategy is to identify the specific needs of the organization. This involves assessing the current situation, determining the gaps that need to be filled, and prioritizing them accordingly.
Develop a Plan
Once the needs have been identified, the next step is to develop a comprehensive plan. This plan should outline the steps required to implement the temporary replacement, including timelines, resource allocation, and contingency measures.
Benefits and Challenges of Temporary Replacement
Temporary replacement [EP 3] offers numerous benefits, but it also comes with its own set of challenges. Below is an overview of both:
Benefits
- Cost savings: Temporary replacements often come with lower costs compared to permanent solutions.
- Flexibility: They allow organizations to adapt quickly to changing circumstances.
- Improved productivity: By maintaining operations during disruptions, temporary replacements help boost overall productivity.
Challenges
- Integration: Ensuring that temporary replacements integrate seamlessly with existing systems can be challenging.
- Quality control: Maintaining quality standards when using temporary resources is crucial but can be difficult.
Best Practices for Temporary Replacement
To ensure the success of temporary replacements, organizations should adhere to best practices. Below are some recommendations:
Training and Onboarding
Providing adequate training and onboarding for temporary workers is essential. This ensures that they understand their roles and responsibilities and can contribute effectively to the organization.
Regular Monitoring
Regular monitoring of temporary replacements is necessary to identify and address any issues that may arise. This proactive approach helps maintain quality and efficiency throughout the process.
Managing Temporary Replacements in the Workplace
Managing temporary replacements in the workplace requires a delicate balance between efficiency and empathy. Below are some tips for effective management:
Clear Communication
Clear communication is key to managing temporary replacements successfully. Ensure that all stakeholders, including permanent employees, are aware of the reasons for the replacement and the expected duration.
Set Expectations
Setting clear expectations for temporary workers is crucial. This includes outlining their roles, responsibilities, and performance metrics, ensuring that they understand what is expected of them.
Case Studies of Successful Temporary Replacements
Several organizations have successfully implemented temporary replacements to address various challenges. Below are two case studies:
Case Study 1: Healthcare Industry
In the healthcare industry, temporary replacements are often used to manage staffing shortages during peak periods. A hospital in California implemented a temporary staffing solution during the flu season, resulting in improved patient care and reduced wait times.
Case Study 2: Manufacturing Sector
A manufacturing company in Germany faced a significant equipment failure that threatened to halt production. By deploying a temporary replacement machine, they were able to maintain production levels while the original equipment was repaired, minimizing financial losses.
Conclusion
Temporary replacement [EP 3] is a vital concept that has evolved over time to meet the needs of modern organizations. By understanding its importance, implementing effective strategies, and adhering to best practices, organizations can ensure that temporary replacements contribute positively to their operations.
We invite you to share your thoughts and experiences with temporary replacements in the comments section below. Additionally, feel free to explore other articles on our site for more insights and strategies. Together, let's continue to build a more adaptable and resilient future!

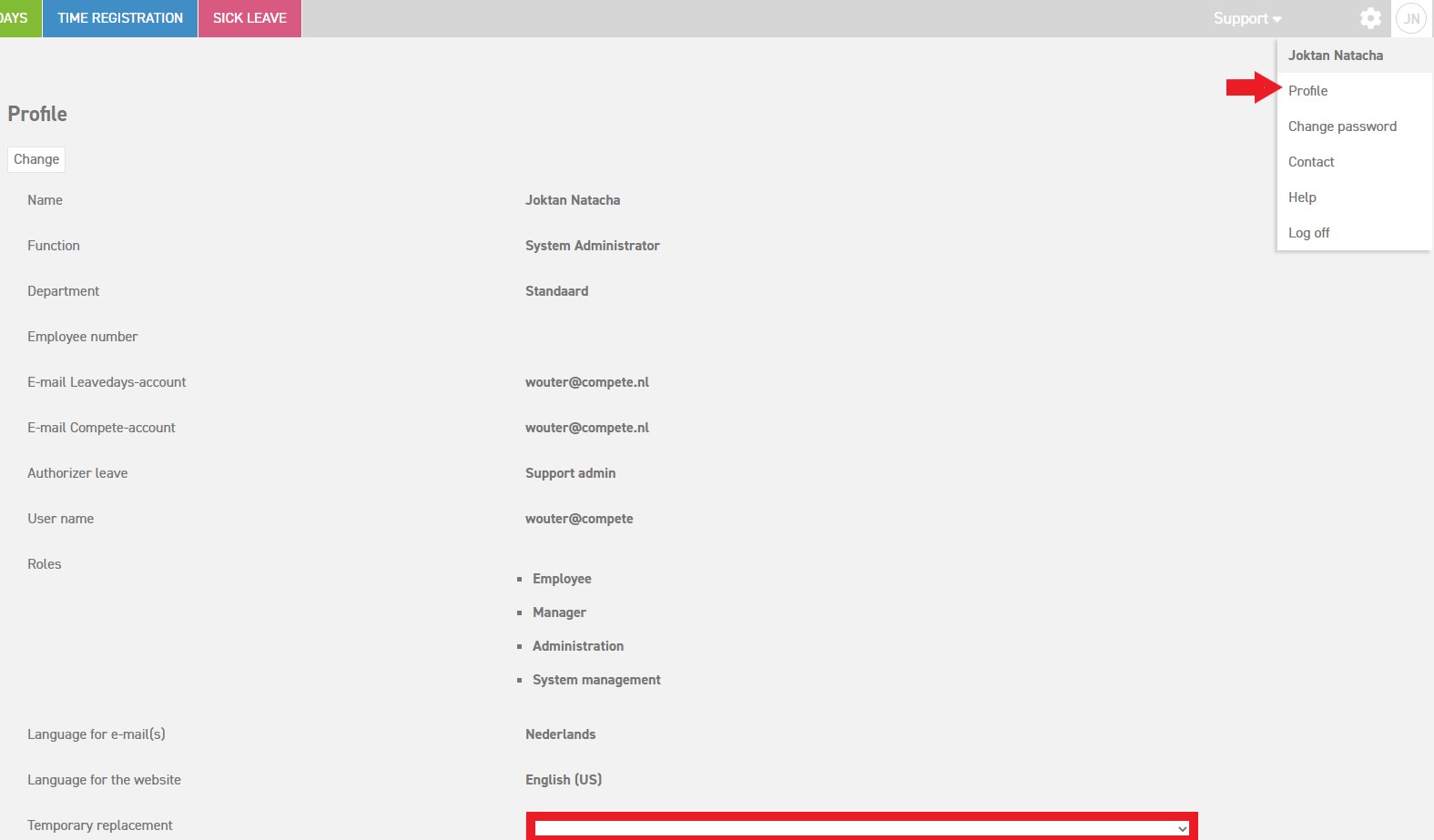
![Temporary Replacement [EP 2] The Essential Guide](https://i.ytimg.com/vi/p4vp056-Suo/maxresdefault.jpg)